
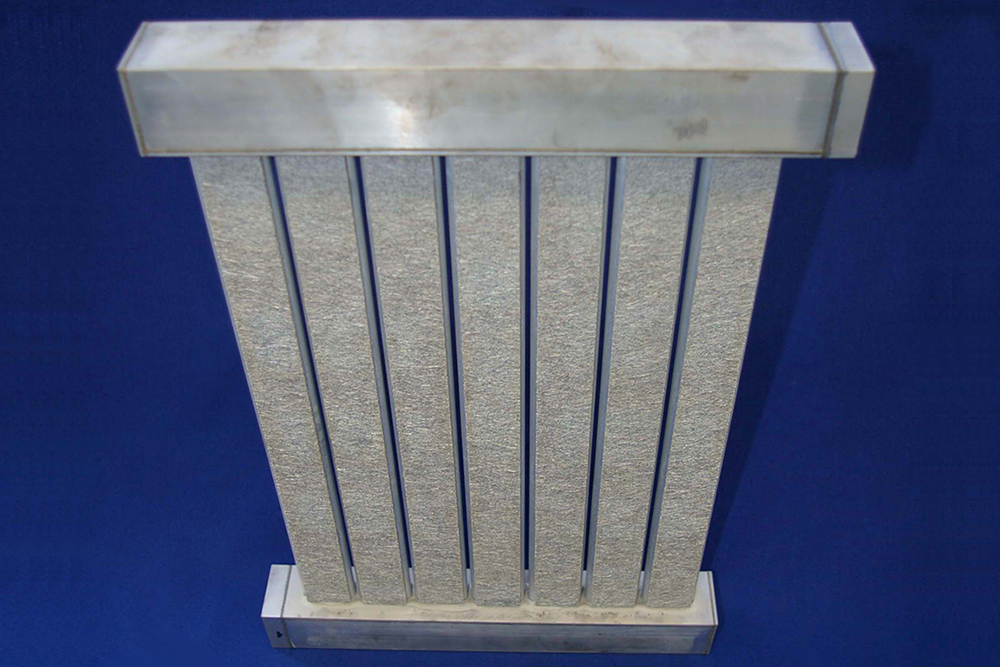
Aluminium-Faserstrukturen für hocheffiziente Wärmepumpen
Im Rahmen des BMWi-geförderten Projektes »Entwicklung einer Gasadsorptionswärmepumpe mit einem aufkristallisierten Zeolithwärmeübertrager und einem neuartigem Verdampfer-Kondensatorapparat (ADOSO)« entwickelt das Fraunhofer IFAM in Dresden zusammen mit der Stiebel Eltron GmbH und der Sortech AG sowie dem Fraunhofer ISE in Freiburg eine hocheffiziente Adsorptions-Wärmepumpe für die Bereitstellung von Warmwasser und Heizenergie in Wohngebäuden.
Effiziente Techniken für die Bereitstellung von Warmwasser und Heizenergie in Wohngebäuden sind ein wichtiger Baustein für eine ressourcenschonende Energieversorgung. Wärmepumpen nutzen dafür Umweltwärmequellen wie Erd- oder Solarwärme oder auch Umgebungsluft. Üblicherweise werden sie elektrisch betrieben. Um auch für den Energieträger Erdgas eine Nachfolgetechnologie zu den am Markt verfügbaren Gasbrennwertgeräten anbieten zu können, wird bei Gas-Wärmepumpen ein Gasbrennwertgerät mit einem thermisch angetriebenen Wärmepumpenmodul kombiniert.
Ziel des Projekts ADOSO ist daher die Entwicklung eines Heizgeräts auf Zeolith-Basis mit Wasser als Arbeitsmittel, welches auf Grund neuartiger Adsorptionswärmeübertrager und der optimierten Funktionsweise von Verdampfer und Kondensator bei vergleichbaren Leistungen und einer Jahresarbeitszahl von über 1,3 deutlich kompakter und kostengünstiger als die am Markt befindlichen Geräte ist.
Für die Entwicklung des Adsorptionswärmeübertragers sind poröse, aber dennoch gut wärmeleitende Materialien mit einer hohen beschichtbaren Oberfläche von zentraler Bedeutung. Am Fraunhofer IFAM wurden dafür Strukturen aus versinterten Aluminiumfasern entwickelt. Die Kurzfasern aus der Legierung AlSi1 werden durch Flüssigphasensintern stoffschlüssig miteinander verbunden. Auf diese Weise entstehen offenporöse Strukturen mit sehr hohen spezifischen Oberflächen, auf die der Zeolith aufkristallisiert wird. Durch den hohen Porenanteil von 75 % wird ein guter Zutritt des Wasserdampfes an die Zeolith-Oberflächen auch im Inneren der Strukturen ermöglicht. Am Zeolith wird der Wasserdampf eingelagert und setzt dabei eine extrem große Wärmemenge frei, die über die Aluminium-Faserstruktur an wasserführende Rohre abgegeben wird. Bei der Desorption des Wasserdampfes wird dieser Prozess umgekehrt und dem Zeolith Wärme zugeführt, so dass die Wasserdampfmoleküle wieder aus dem Zeolith freigesetzt werden.
Die große Oberfläche des Metallfaserwerkstoffs gepaart mit der dünnen Zeolith-Schicht beschleunigt die Dynamik der Ad- bzw. Desorption des Wasserdampfes erheblich gegenüber dem Stand der Technik und ermöglichte bei dem bislang getesteten, nicht weiter optimierten ersten Prototypen bereits eine Verdoppelung der Leistungsdichte auf 300 W/l. Die Realisierung kompakter und preisgünstiger Adsorptions-Wärmepumpen rückt damit in greifbare Nähe. Da sich dieses Wärmepumpenprinzip auch für die Kälteerzeugung mittels Abwärme eignet, eröffnet sich auch hier ein interessanter Markt. Aus diesem Grunde plant die Sortech AG, in Kürze mit Feldtests der neuen Adsorber-Generation in ihrer eigenen Kältemaschinen-Produktlinie zu beginnen.